企業のホームドクターとして、お困りの問題をワンストップサービスで解決
エンタープライズ ソリューション(開発事例)
- Home
- エンタープライズソリューション
本当に必要な「ソリューション=解決策」をご提案します!
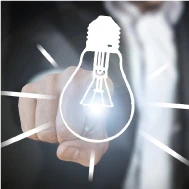
業種・業務別ノウハウ
創業48年、さまざまな業種・業務のシステム開発を経験してきたノウハウがあります。
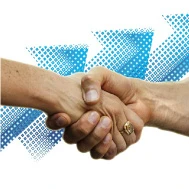
より良いご提案
独立系システム開発会社(SI)のため、メーカーにとらわれることなく、ご要望に応じてより良いご提案が可能です。
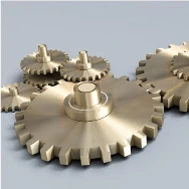
カスタマイズ自在
先端技術を積極的に取り入れており、カスタマイズにも柔軟に対応します。
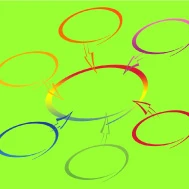
ワンストップサービス
ハードウェア・ソフトウェアともに、さまざまな技術者が揃っています。開発から運用までワンストップで支援いたします。
実績は100例以上、まずはお気軽にご相談ください。
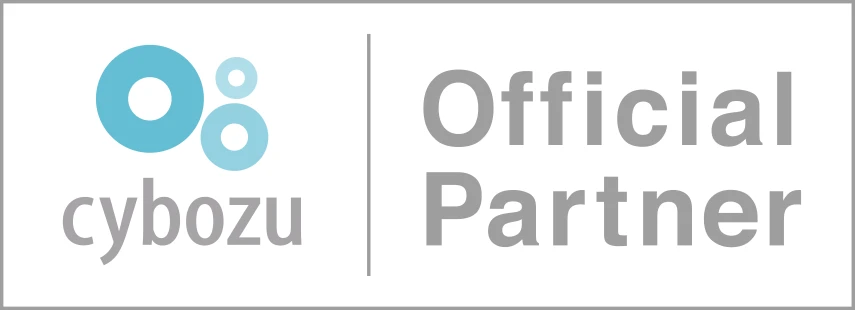
kintone (キントーン) による業務アプリ開発
kintoneはサイボウズ株式会社が提供するビジネスアプリ作成クラウドで、管理系のシステム(販売管理、営業管理、製造管理、経費管理など)を簡単に開発できる「高速開発ツール」です。
当社は「Cybozuオフィシャルパートナー」として、「kintone」による基幹システムの提案を行っています。
kinterp
おすすめ!
業務アプリ開発プラットフォームの「kintone」にERPの要素を加えた業務システム。多業種で使用可能な様々なテンプレートをkintone上で展開。本格的な業務システムを迅速に構築可能。
kinterpの専用サイトを見る
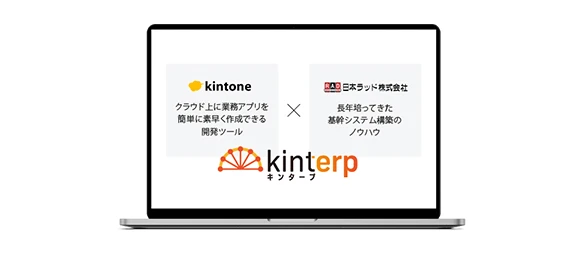
kinterp DB
kintoneとRDBMSの双方向でデータの自動同期が可能。それにより、RDBMS上でのバッチ処理によるデータ集計、更新も可能になります。また、他のシステムとの連携も柔軟に構築でき、kintoneの活用範囲がぐっと広がります。
kinterp DBの専用サイトを見る
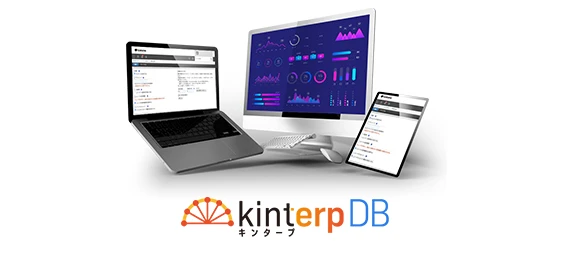
COBOLからJavaへ、レガシーシステムを自動で変換
TSRI JANUS Studio®
世界200社以上が採用し250プロジェクト以上を成功に導いてきTSRI社の自動変換ツール「JANUS Studio®」と日本ラッドの「50年のシステム開発実績とノウハウ」を活用して、レガシーシステムからのマイグレーションを実現し、2025年の崖問題の克服をサポート。
TSRI JANUS Studio®の専用サイトを見る
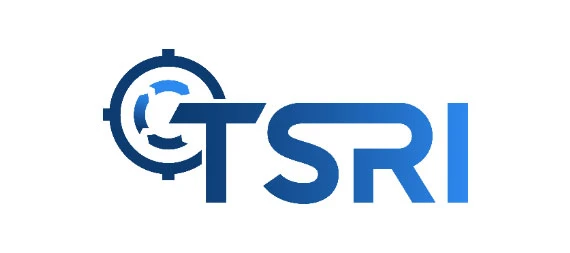
Excel業務を効率化
Excelを入出力インターフェイスとしたデータベースアプリケーションで、既存のExcel利用を継続したまま、データを収集、管理する仕組みをご提供します。
電話とWEBで24時間・365日完全無人対応の予約システム
トルテル® for マイナカード(電話&WEB対応)
【自治体様向け】マイナンバーカード発行予約者様と自治体様の受け渡し予約を簡潔にかつスピーディに行っていただける、24時間・365日電話&WEB対応 完全無人の来庁日時予約システムです。
トルテル® for マイナカード(電話&WEB対応)
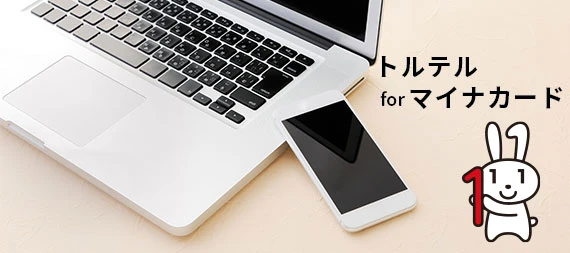
トルテル®α/トルテル®(電話対応)
【自治体様向け】トルテル® α/【医療機関様向け】トルテル®
主にクリニック様向けであるコロナワクチン予約システム「トルテル®」を集団ワクチン接種時に要求される要素を自治体様に向け機能強化した「トルテル® α」。
トルテルα/トルテルの詳細を見る
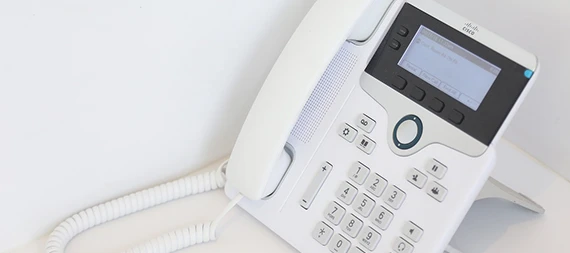
ソリューション実績
その他の実績
ソリューション | 業種 |
---|---|
金融情報配信GWシステム | 金融 |
カード業務システム | 金融 |
UNISYS DB → IBM DB (TOTAL)へのデータ移行 | 金融 |
リスク管理システムIFシステム | 銀行 |
車両管理システム | 銀行 |
日銀 - 銀行間のシステム | 銀行 |
海外拠点システム | 信託銀行 |
リスク管理システム | 信託銀行 |
ソリューション | 概要 | 業種 |
---|---|---|
産業用スマートタッチパネル |
8.5インチワイドカラー液晶タッチパネルを装備した一体型スマートタッチパネルモニタ。 表面防塵・防滴仕様のため、産業・工業用の監視モニタやGPS機能 を内蔵し簡易ナビなどにも最適です。 外部通信は3GModem・Ethernet・RS485などを用途に応じた選択、 HDMI/RGB経由での外部モニタへの出力もできます。 自社での設計・製造のため、産業用製品として長期安定供給ができます。 モニタの取付けはパソコンモニタと同一規格(VESA)を採用しているため、 市販の取付け金具を流用することができます。 |
|
光学フィルム製造会社向け工場自動化(FA)システム | 工場内の生産機械と自動倉庫間および入出荷口との間で、材料/製品を無人搬送し、省力化から在庫管理までをトータルに行うFA(Factory Automation)システムで、業務効率の向上を図ります。 | |
企業内ネットワーク上に設置されているプリンタを 検索・管理するシステム |
メーカー | |
在庫管理など | 自動倉庫への入出庫制御、HTによる入出荷検品、上位システムとの連携 | メーカー |
輸出システム内のEDIインターフェース | メーカー | |
ERPを使用した業務支援レポートの開発 | メーカー | |
需給計画、発注支援システム構築 | メーカー | |
生産管理システム | 金属 | |
工事原価・会計システム | 建設 | |
受注連携(EDI)システム | BACREX(パッケージ)を利用し、取引先からの受注情報をHOST側へ取込むEDIコントロール開発 | 建設材料製造 |
原価管理システム | HOST側で管理する、製品、部品、加工費情報などを月次で取り込み、原価管理を実現するシステム | 部品製造 |
納豆製造の生産管理システム | 食品 | |
ECサイト、通販システム | Perl によるフルスクラッチでの開発と立ち上げ | 食品 |
BPCS導入 | 富士通HOST → AS400へのデータ移行 | 音響機器 |
新生産管理システム | 印刷 | |
市販後調査管理システム | 製薬 | |
医薬情報部門システム | MRからの問合せ内容管理 | 製薬 |
製造販売後調査進捗システム | 製薬 |
ソリューション | 概要 | 業種 |
---|---|---|
在庫管理など | 自動倉庫への入出庫制御、HTによる入庫設定、上位システムとの連携 | 運送 |
伝票発行システム、得意先毎に指定した伝票に印刷を行うシステム | 運送 | |
需給計画システム | 商品の在庫、販売実績より需給予測を計算し、適切な在庫日数を保つ輸送計画を行うシステム | 物流 |
出荷、梱包、検品システム構築、ハンディーターミナル対応 | 自動倉庫への入出庫制御、HTによる入出荷検品、上位システムとの連携 | メーカー |
新食材システム | 食材宅配 |
ソリューション | 概要 | 業種 |
---|---|---|
花卉ブロードバンドオークションシステム | 衛星放送と専用端末を使用していた既存の花卉(かき)仕入れのシステムを、インターネット環境があればどこでも競売に参加出来るように構築し、花卉仕入れの利便性向上を実現 | |
流通・卸売り・小売業向けEDIシステム | インターネットEDIシステムBACREX導入 | |
販売管理システム | 家電 | |
注文品支援システム | 出版物専門商社 | |
薬品販売管理システム | 商社 | |
ポイント会員の購買データを元に、売上を分析する情報管理システム | 小売 | |
POS切替における基幹システムとのI/F開発 | 小売 | |
蓄積された膨大な販売データ(DWH)を基にした、経営層向けのデータ分析システム | 医薬品 | |
販売日管理システム | たばこ |
ソリューション | 概要 |
---|---|
ECサイト |
大手小売店向けECサイト刷新プロジェクトで外部システム連携機能の開発、およびデータ移行を担当。 また、食品会社向けのECサイトも構築。会員登録、商品注文(お買い物かご~注文完了)、マイページおよび各種マスタメンテナンスなどのバックオフィス機能。通常のECサイトをフルスクラッチで構築。 |
電子決済システム |
ソリューション | 業種 |
---|---|
総合カーリースシステム | リース |
建設機器リース在庫管理システム | リース |
リース会社向け車両管理システム | ソフト |
レンタカー貸渡・管理システム | レンタカー |
空港の輸出入貨物を管理するC/Sシステム | 航空 |
新国内精算管理システム | 航空 |
搭乗予約者の人数等の情報から、機内食の献立作成・発注・受注・納入まで行う統合システム | 航空 |
ソリューション | 概要 | 業種 |
---|---|---|
GISマッピングシステム | GIS(地理情報システム)と連動して、不動産や占有物などを地図上にマッピングするシステム。 当社は20年以上前からGIS技術に力を入れており、各地の自治体や公共機関、企業にて利用される地図連動システムも数多く手がけています。 | |
CBT 予約受付システム | CBT(資格試験のプロセスをコンピュータ化するサービス)における 予約受付システム | CBT運営 |
電子書籍、占いなどのデジタルコンテンツ販売システム | ISP | |
顧客管理システム | ネットワーク販売 | |
竣工データ移行システム開発 | 通信 | |
道路上、道路下の占有物を管理するマッピングシステム | 通信 | |
通信会社の社内設備を管理するマッピングシステム | 通信 | |
移動通信会社向け販売管理システム | 通信 | |
予実管理システム | 営業支援システムで管理する、販売予測、販売実績を日次で取り込み、予算との達成率を管理するシステム | 通信 |
業務支援システムのマイグレーション | 携帯電話販売管理のためのシステム | 通信機器販売 |
ソリューション | 業種 |
---|---|
WEB受注システム | プラント |
公共案件の見積、入札、契約~納品、請求までの情報を管理するWEBシステム | メーカー |
Web勤怠管理システム | 販売 |
携帯電話からのアクセスでキャリアのWebメニューを表示するシステム | 通信 |
ソリューション | 概要 |
---|---|
ライブ映像アーカイブシステム | ライブ動画を、インターネットで配信しながらリアルタイムにアーカイブ(録画)してオンデマンド動画配信にも対応するシステム。プロスポーツのライブ映像配信等で使われています。ライブ映像にリアルタイムでテロップを挿入したり、過去のコンテンツにタグ付けして検索しやすくしたりと便利な機能も装備 |
オンラインゲームの配信バックエンドシステム | 日本および米国で技術特許を取得したP2P型配信システム「グリッド・デリバリー(Grid Delivery®)」を利用し、DVDまるごと1枚分の大容量のデータを最大数万人規模の同時接続で配信しています。 |
動画配信システム | |
ライブ配信システム | |
映像レコーディングシステム | |
DRMシステム(Marlin、Microsoft) |
ソリューション | 概要 | 業種 |
---|---|---|
どこでもバス (デマンド交通システム) | 全国57以上の自治体にて導入されている業界トップシェアのコミュニティバス運行支援システムです。 地元のタクシー会社や自治体の小型乗り合い自動車で、利用者を自宅から目的地まで送迎する新しい交通システムです。 バスのような低料金で、タクシーと同様にドア to ドアを実現する便利な交通手段として、路線バスのない過疎地や高齢者の多い地域はもちろん、都市部のコミュニティバスシステムとしても期待される、次世代交通支援システムです。 | |
緊急車両向けカーナビシステム (車両運用端末装置) |
本部の情報システムと連携し、災害地点、自車位置、災害時の出動指令情報、各種支援情報 および現場活動状況をリアルタイムに情報交換し、 車両運用の効率化と現場の情報武装による活動支援を行います。また、目的地(災害現場・病院など)へのナビゲーション機能の提供および住宅地図、道路地図、防火対象物や危険物などの 支援情報の提供、現場到着途上における部所位置予約機能や 他車両との情報共有、搬送先病院の検索など様々な用途に対応します。 | |
電子図書館システム | 図書データの収集登録業務、業務運用管理システム、館内および外部と連動した図書検索システム など、図書館に必要な各種業務システム一式です。形態素解析による検索システムのパフォーマンス向上など、独自の工夫もたくさん盛り込まれています。 | |
流通情報システム | ガス | |
日本全国から寄せられる苦情やトラブルの内容を瞬時に検索するシステム | 行政法人 | |
GISマッピングシステム | 道路上、道路下の占有物を管理 | 財団法人 |
上下水道検針システム | 上下水道料金の検針から収納までの水道業務を管理するシステム。定型処理業務である検針~収納~停水までの業務、また随時発生する照会業務、開閉栓業務や、年次処理の業務を行うための機能を持つ。 | 地方自治体 |
受発注業務における社内原価管理システム | 電気設備 | |
IBMパッケージ(New Const Pack)の導入とカスタマイズ | 電気設備 | |
電力会社の発電所を点検整備する工事の精算を実行指示するシステム | 電力 |
ソリューション | 概要 | 業種 |
---|---|---|
C/Sシステム | ツアーを構成するホテルや車などの仕入を管理 | 旅行 |
C/Sシステム | 個人のツアー申込者の情報や申込者に対する販売管理 | 旅行 |
C/Sシステム | ツアーで利用したホテルや車などの精算金額、および旅行代理店へ請求するツアー代金を管理 | 旅行 |
国内旅行システム改修 | 決算期変更に伴うシステム改修 | 旅行 |
店舗(パチンコ店)の売上情報参照や請求書発行を行うシステム | アミューズメント |
ソリューション | 概要 | 業種 |
---|---|---|
賃貸業務予実管理システム | 賃貸業務の予算と実績を管理 | 不動産 |
基幹システム再構築によるデータ移行システム | 保険 | |
地方自治体向け財務会計システム | 会計 | |
人材派遣システム | 支払・請求、人事・給与管理を一元的に管理するシステム | 派遣 |
主なハードウェア開発事例
下記以外の実績や、各ケースの詳細は、当社までお問い合わせください。
消防・防災系
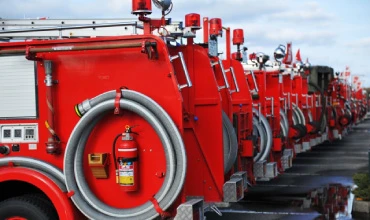
- 緊急車両用 情報端末装置
- 消防システム
- 防災システム
計測・制御系
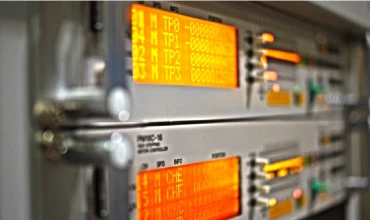
- ガラスびん色選別装置
- 新幹線、在来線駆動系試験装置
- 半導体超音波洗浄制御システム
- ウレタンフォーム発泡制御装置
- パイプベンダー制御装置
- 牛肉質判定自動化システム
- 海底地震データロガー
- ゴルフ場散水システム
- ページプリンター制御装置
- 原子力発電所総合警戒システム
情報・通信系
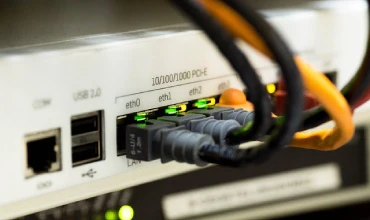
- L2スイッチ
- WCDMA携帯電話
- セットトップボックス
- IP電話機
- MCA無線機
- デジタル交換機
- 音声/FAX蓄積システム
- 自動音声応答システム
- 電話録音・再生装置
- 海外旅行傷害保険発券機
- 有線回答システム
- 外食向けオーダー端末
医療系
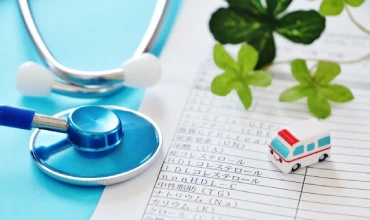
- 自動再診受付機
- 受付状況表示システム
- 入金機処理システム
- 院内事務処理システム
- 順番券発行機
- 社員健康診断システム
- 臨床検査システム
自動車・船舶・産業系
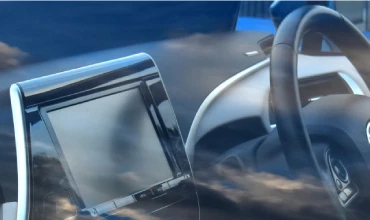
- カーナビゲーション システム
- カーオーディオ システム
- ディーゼル排気ガス低減制御用ECU
- 産業用スマートタッチパネルモニタ
エンジニア・プログラマ派遣、システムエンジニアリング・サービス
当社には正社員の技術者が約300名在籍しています。
幅広い業種・業務、あらゆるIT領域に対してエンジニアを派遣、設計~製造(コーディング)~保守・運用フェーズまでサポートしています。
当社に在籍するエンジニア(いずれも正社員)の主な開発スキルをご紹介します。
下記以外のサービスやサービスの詳細は、当社までお問い合わせ下さい。
分類 | 環境、ミドルウェア | 言語 | |
---|---|---|---|
業務アプリケーション | インターネット系、クライアント/サーバ系、ホスト系、TANDEM業務/通信系、ERP | Linux、Windows、HP-UX、Solaris、IBM AIX、BSD、OS/2、OS/400、ACOS4、z/OS、VOS3、NonStepOS、MacOS/iOS、Android、etc. ミドルウェア: apache、IIS、tomcat、WebSphere、Cold Fusion、DB2、Informix、Sybase、Oracle、MySQL、PostgreSQL、Microsoft SQL server、Access、IMS/DB、DL/I、VSAM、RIQS、ADBS、etc. |
C、C++、Objective-C、C#、VB、VB.net、ASP、Java、Perl、PHP、Ruby、Python、COBOL、PL/I、Fortran、RPG、Delphi、Progress、TAL、ABAP、Developer 2000、etc. |
制御アプリケーション、ファームウェア、組み込み系 | L2/L3スイッチファームウェア、ルータファームウェア、PBX/IP電話ファームウェア、カーナビ、GPSシステム、各種表示端末、STB(セットトップボックス) | Linux、Windows、HP-UX、Solaris、IBM AIX、MacOS/iOS、Android、iTRON、BTRON、DR-DOS、MS-DOS、VRTX、VXWORKS、MACH210、FLEX 6000 /8000 /10K10 /10K30、XC4025/4062、L4MXX、etc. | C、C++、C#、VB、VB.net、Java、ASM、VHDL、etc. |
Webアプリケーション | ECシステム、電子決済システム、動画配信システム、ライブ配信システム、映像レコーディングシステム、DRMシステム(Marlin、Microsoft) | Linux、Windows、MacOS/iOS、Android、etc. | C、C++、C#、VB、VB.net、Java、Perl、PHP、Ruby、Python、etc. |
モバイルアプリケーション | 携帯電話、iPhone、Android | iOS、Android、Symbian、Windows Embedded、iTRON、etc. | C、C++、Objective-C、Java |